Understanding Plastic Injection Molders: Transforming the Manufacturing Landscape
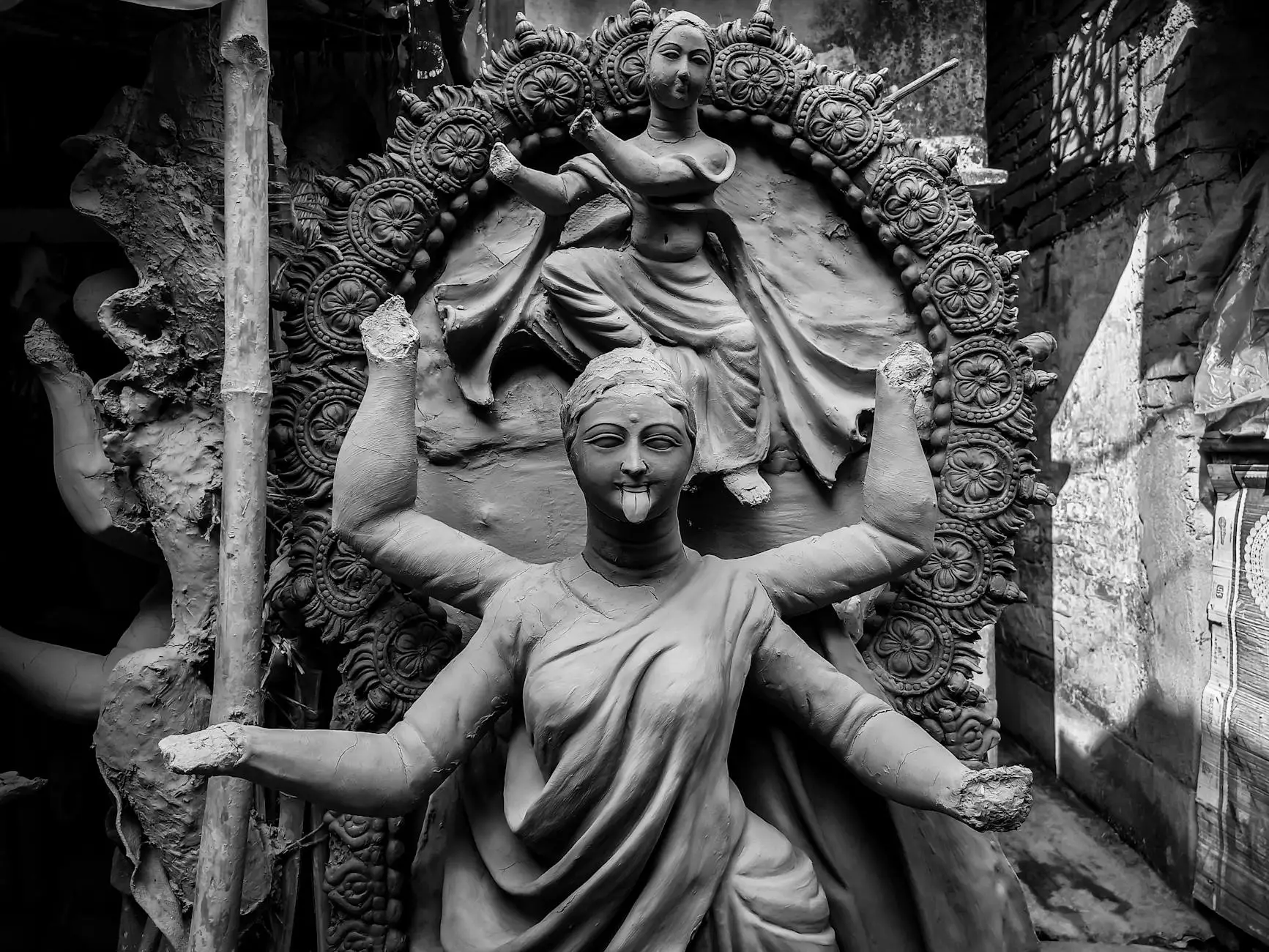
In the competitive world of manufacturing, one technique has risen to prominence for its efficiency and versatility: plastic injection molding. This process is pivotal in creating a myriad of plastic products, from household goods to intricate components utilized in high-tech devices. With the global market for plastic molding on the rise, it is essential to delve deeply into the intricacies of plastic injection molders and understand their role in the industry.
The Basics of Plastic Injection Molding
Plastic injection molding is a manufacturing process used for producing parts by injecting molten material into a mold. It is renowned for its ability to create complex and precise shapes with high repeatability, making it an ideal choice for mass production. Here is a breakdown of the fundamental stages involved in the process:
- Material Selection: The first step involves selecting the appropriate type of plastic material according to the product's needs, be it thermoplastics, thermosets, or elastomers.
- Mold Design: A critical phase where engineers design a mold that meets the product specifications, ensuring optimal flow and cooling characteristics.
- Injection Process: Once the mold is prepared, the selected plastic is heated until it melts and is then injected into the mold under high pressure.
- Cooling and Solidification: The molten plastic is allowed to cool and solidify inside the mold, taking on its shape.
- Product Removal: After cooling, the mold is opened, and the finished product is ejected, often requiring minimal finishing work before it can be packaged and shipped.
The Advantages of Using Plastic Injection Molders
Plastic injection molding offers a variety of advantages that make it a favored choice among manufacturers:
- High Efficiency: The process is highly automated, allowing for rapid production rates and reduced labor costs.
- Precision and Consistency: Molds can create incredibly precise components that are uniform in quality, meeting strict industry standards.
- Design Flexibility: Complex geometries and detailed features can be achieved, opening the door to innovative product designs.
- Material Versatility: A wide range of plastic materials can be utilized, including reinforced and engineering plastics that enhance product performance.
- Reduced Waste: The process is highly efficient, and any excess plastic can be recycled, which contributes to more sustainable manufacturing practices.
Current Trends in Plastic Injection Molding
The field of plastic injection molding is continuously evolving, driven by technological advancements and changing market demands. Here are some notable trends that are shaping the future:
1. Automation and Industry 4.0
The integration of automation and smart technologies is revolutionizing the injection molding industry. Manufacturers are increasingly employing robotics, IoT (Internet of Things), and AI (Artificial Intelligence) to streamline processes, enhance productivity, and improve quality control.
2. Sustainable Practices
With rising environmental consciousness, many manufacturers are adopting sustainable practices in their operations. This includes utilizing biodegradable plastics and implementing recycling programs to reduce plastic waste.
3. Customization and On-Demand Production
As consumer preferences shift toward customization, plastic injection molders are responding by offering more flexible production solutions that cater to specific customer needs, including short-run production and bespoke designs.
The Role of Metal Fabricators in Plastic Injection Molding
While plastic injection molding is at the forefront, it is essential to recognize the vital role of metal fabricators in this ecosystem. Metal fabricators contribute to creating molds that are crucial for the injection molding process. Their expertise in machining, welding, and metal assembly ensures that the molds are durable, precise, and capable of withstanding the rigors of mass production.
How Metal Fabrication Supports Plastic Injection Molding
- Durability and Strength: Metal molds are more resilient than plastic molds, capable of producing thousands of units without degradation.
- Precision Engineering: Metal fabricators utilize advanced machining techniques to create molds with high tolerances and intricate designs.
- Heat Management: Metal molds provide superior thermal conductivity, facilitating efficient cooling cycles during production.
Finding the Right Plastic Injection Molder
Choosing the right plastic injection molder is crucial for any business looking to streamline its manufacturing processes. Here are some key considerations to keep in mind:
1. Experience and Expertise
Look for a team with a proven track record in the industry. Experience often correlates with proficiency in problem-solving and innovation.
2. Technology Adoption
Assess their investment in modern technologies and practices. Companies that embrace cutting-edge techniques tend to produce higher-quality products and more efficient processes.
3. Customer Service and Support
A responsive and knowledgeable customer service team can significantly enhance your working experience, especially when facing unique project challenges.
Case Studies: Successful Applications of Plastic Injection Molding
To help illustrate the effectiveness of plastic injection molding, here are a few case studies showcasing its applications:
Case Study 1: Automotive Industry
The automotive sector is a leading adopter of plastic injection molding. For instance, several manufacturers utilize this technique to produce dashboard components that demand high precision and durability, thus enhancing both safety and aesthetic appeal.
Case Study 2: Consumer Electronics
In the realm of consumer electronics, plastic injection molding is instrumental in creating lightweight and robust connectors, casings, and internal parts that optimize device performance and ensure user comfort.
Case Study 3: Medical Devices
The medical field benefits immensely from plastic injection molding, particularly in producing sterile disposable products such as syringes and surgical instruments, which require stringent compliance with health regulations and standards.
Conclusion
As the landscape of manufacturing continues to evolve, plastic injection molders stand at the forefront of innovation and efficiency. Understanding their processes, advantages, and the integral role of metal fabricators provides valuable insights for businesses looking to enhance their production capabilities. By leveraging these technologies and considering sustainability and customization trends, companies can position themselves for future growth in an ever-competitive market.
For businesses seeking tailored solutions in plastic injection molding, look no further than deepmould.net, where expertise meets innovation in the realm of manufacturing.