Understanding Precision CNC Machining Suppliers
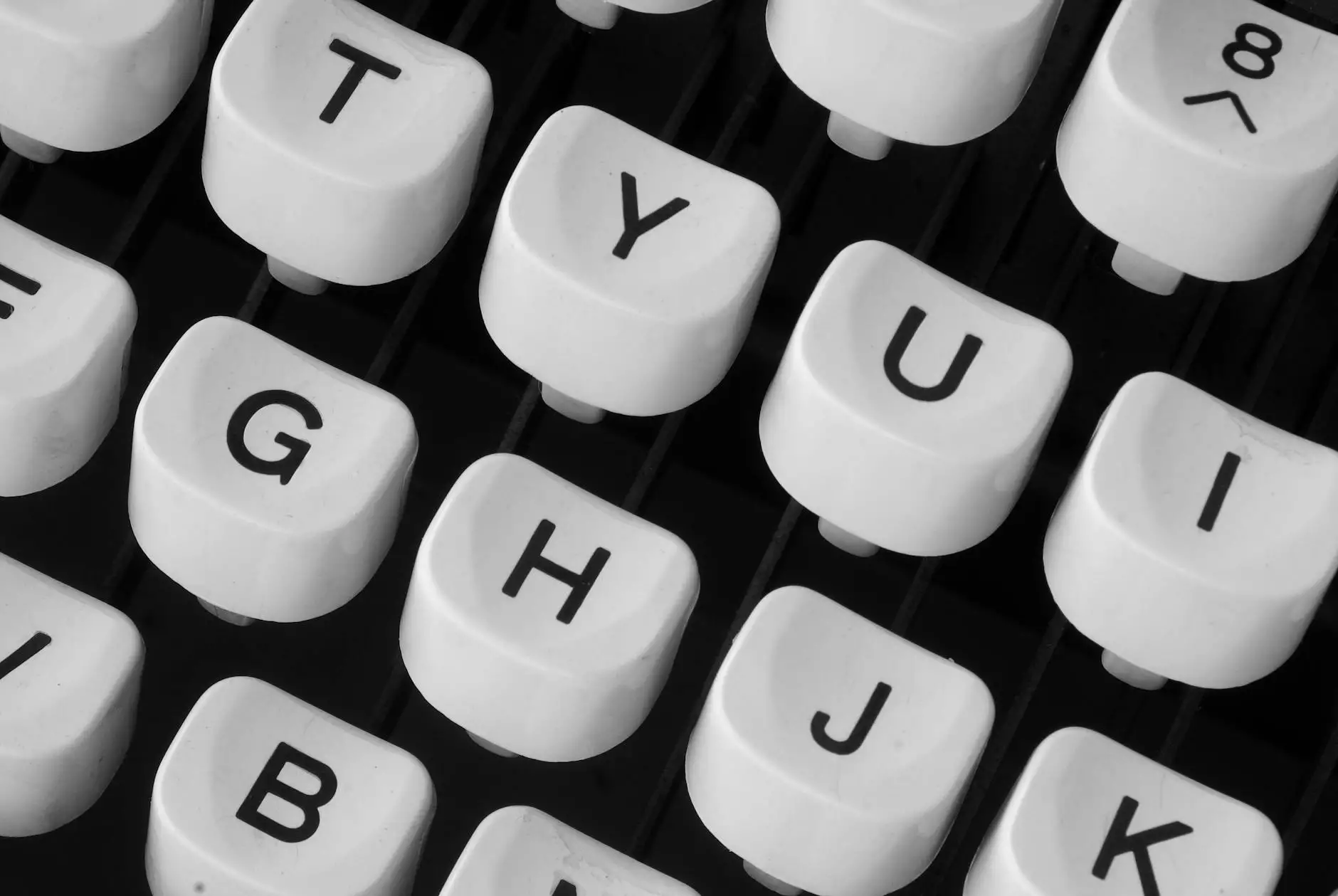
Precision CNC machining has revolutionized the way metal fabricators operate, offering accuracy, efficiency, and the ability to produce complex components with ease. This article will delve deep into the realm of precision CNC machining suppliers, examining their role in metal fabrication, key benefits, and how to select the right supplier for your specific needs.
The Importance of Precision CNC Machining
CNC machining stands for Computer Numerical Control machining, a process that utilizes computers to control machine tools to achieve precise cuts and shapes. This technology is essential in various industries, from aerospace to automotive, and has grown exponentially in recent years. The significance of precision CNC machining lies in its ability to produce parts that meet stringent specifications and tolerances.
Key Benefits of Precision CNC Machining
- Enhanced Accuracy and Consistency: CNC machines operate with high precision, ensuring that every component produced is consistent in quality.
- Complex Shapes Made Simple: CNC technology allows for the crafting of intricate designs that would be difficult to achieve through manual machining.
- Reduction in Waste: The accuracy of CNC machining minimizes material waste, making it a cost-effective solution for manufacturers.
- Increased Efficiency: CNC machines can run continuously, significantly speeding up the production process.
- Customization: Precision CNC machining allows for easy customization of parts to fit unique designs and specifications.
Choosing the Right Precision CNC Machining Suppliers
With the importance of CNC machining established, the next step is selecting the right precision CNC machining suppliers. The success of your project hinges on the supplier’s capability to meet your specific requirements.
1. Expertise and Experience
Seek suppliers that have extensive experience in the industry. A seasoned supplier will have a deep knowledge of various materials and machining processes, which is crucial for advising clients on the best choices for their projects.
2. Technology and Equipment
The level of technology and the condition of machinery can greatly impact the quality of the output. Suppliers should employ state-of-the-art CNC machines capable of handling your specific machining needs. Investigate whether they utilize the latest software and machining techniques to stay ahead in the market.
3. Quality Control Processes
Reputable suppliers prioritize quality control to ensure that every product meets or exceeds expectations. Look for suppliers with established quality assurance procedures, including inspection and testing of components.
4. Client Testimonials and Case Studies
Review feedback from previous clients to gauge the supplier’s reliability and service quality. Case studies showcasing successful projects can provide insights into their problem-solving capabilities and customization skills.
5. Customer Service
Effective communication is vital in any business relationship. A supplier that provides excellent customer service will be more responsive to your needs, which is crucial during critical phases of a project.
Industries Serviced by Precision CNC Machining Suppliers
Precision CNC machining is pivotal in a variety of industries. Precision CNC machining suppliers cater to sectors such as:
- Aerospace: Components must meet strict safety and performance standards.
- Automotive: High volumes of parts require efficiency and precision.
- Medical: Precision machining is essential for creating reliable and safe medical devices.
- Electronics: Precision parts are necessary for the functioning of devices.
- Defense: Critical components demand rigorous oversight and precision.
Cost Considerations in CNC Machining
The cost of machining can vary based on several factors, including material type, complexity of the part, and turnaround time. It’s essential to balance cost with quality when selecting precision CNC machining suppliers.
Factors Affecting Cost
- Material Costs: Higher quality materials will typically increase production costs.
- Complexity of Design: More intricate designs may require additional machining time.
- Production Volume: Larger volumes often lead to lower costs per unit due to economies of scale.
- Lead Times: Rush orders may incur additional fees.
The Future of Precision CNC Machining
As technology continues to advance, the future of precision CNC machining looks promising. Innovations such as artificial intelligence (AI), machine learning, and industry 4.0 are set to streamline processes and enhance efficiency. Suppliers that embrace these technologies will be at the forefront of providing superior machining services.
Emerging Trends in CNC Machining
- Automation: More automated processes will reduce labor costs and increase efficiency.
- Advanced Materials: Innovations in materials will further expand the capabilities of CNC machining.
- Integration with IoT: The Internet of Things will enable better monitoring and optimization of machining processes.
- Sustainable Manufacturing: A focus on environmentally friendly practices will shape future machining processes.
Conclusion
Choosing the right precision CNC machining suppliers is crucial for the success of any manufacturing operation. By understanding the benefits, selecting based on expertise, technology, and client feedback, businesses can harness the power of CNC machining to achieve superior results. As trends evolve, staying informed about new technologies and practices will enable manufacturers to remain competitive in a dynamic market.
DeepMould.net is committed to providing high-quality CNC machining solutions that meet the diverse needs of our clients in the metal fabrication industry. Our experienced team is equipped with the latest technology to ensure precision and efficiency for every project.