Understanding Silicone Membrane for Vacuum Forming
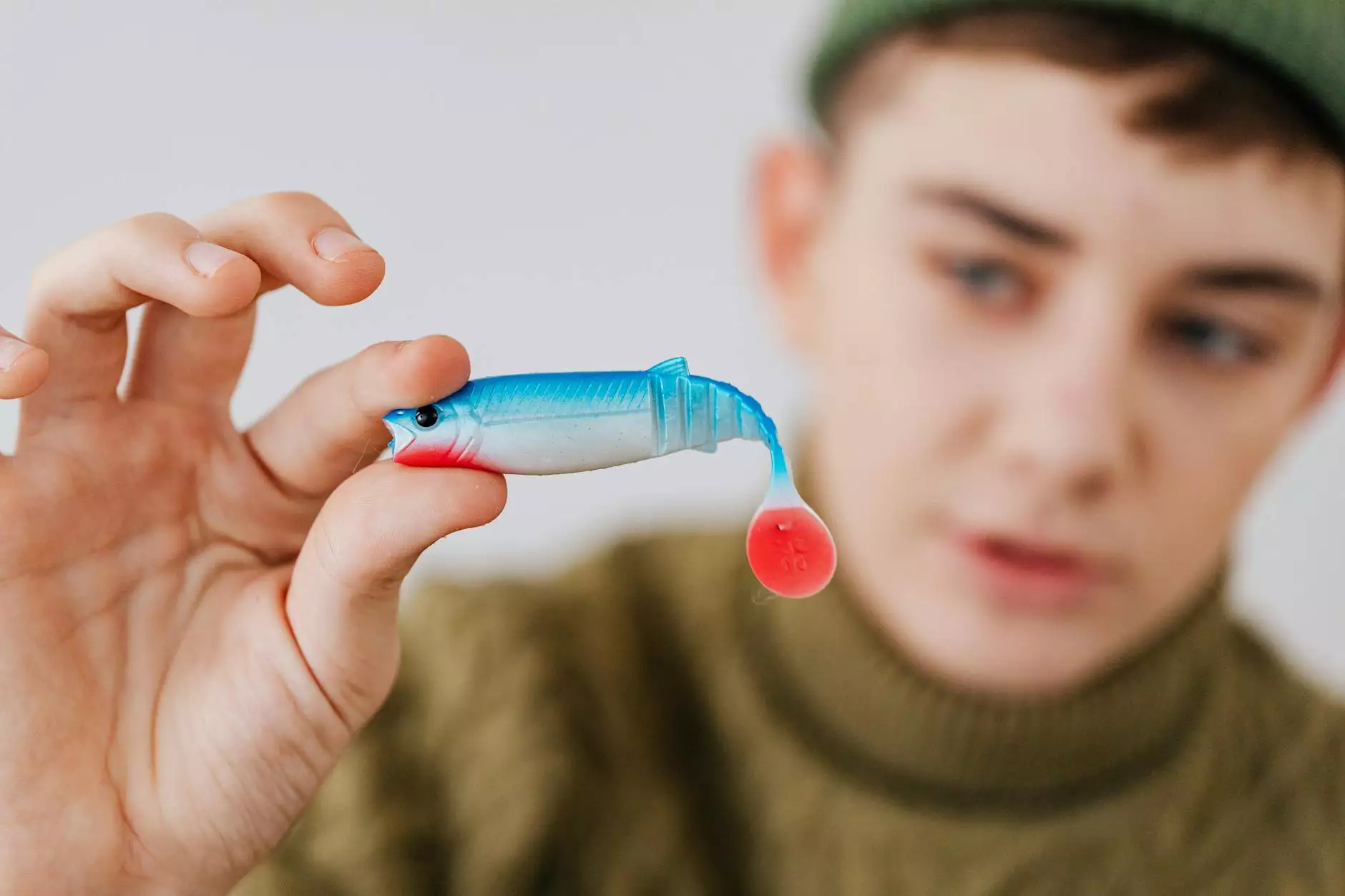
The world of manufacturing is constantly evolving. Among the innovative techniques gaining prominence is vacuum forming, a process that has transformed how we create various products across different industries. At the heart of this process lies a fundamental component that ensures efficiency and precision—the silicone membrane for vacuum forming. In this comprehensive article, we delve into what silicone membranes are, their advantages, applications, and how they serve as a cornerstone in the manufacturing of appliances and cleaning tools.
What is Vacuum Forming?
Vacuum forming is a simplified version of thermoforming. It involves heating a plastic sheet until it is soft and pliable, followed by placing it over a mold. A vacuum is then applied to draw the material onto the mold's surface, creating a precise shape. It is a widely used method for production runs, prototyping, and crafting products for various applications.
Silicone Membrane: The Essential Component
A silicone membrane is a flexible, durable sheet that plays a pivotal role in vacuum forming. These membranes are renowned for their high-temperature resistance, flexibility, and longevity, making them ideal for various applications, particularly in appliances and home cleaning products.
Benefits of Using Silicone Membranes
When opting for silicone membranes in the vacuum forming process, manufacturers enjoy a range of benefits:
- Durability: Silicone membranes can withstand high pressures and repeated use without degrading, leading to lower replacement costs over time.
- Temperature Resistance: Capable of withstanding high temperatures, silicone membranes are suitable for processes involving heated plastics.
- Flexibility: The inherent flexibility of silicone allows it to conform to complex mold shapes, ensuring a tighter seal and improved product quality.
- Easy Cleaning: Silicone membranes are easy to clean, making them ideal for applications in the food industry and home cleaning products.
- Chemical Resistance: They resist a variety of chemicals, reducing the risk of damage during the manufacturing process.
Applications in Appliances and Home Cleaning
Silicone membranes are utilized across a broad spectrum of applications within the appliances and home cleaning categories. Here are some key areas where they excel:
1. Production of Appliance Parts
In the appliance industry, silicone membranes are instrumental in producing components that require precise molding. They are commonly used to create parts for:
- Refrigerators
- Washing machines
- Microwave ovens
- Air conditioning units
The ability to conform to complex shapes allows manufacturers to achieve high fidelity in their products, ensuring each part fits perfectly into the overall appliance.
2. Home Cleaning Devices
In the realm of home cleaning, silicone membranes play a vital role in the fabrication of products like:
- Vacuum cleaners
- Steam mops
- Pressure washers
Their flexible nature helps in creating seals that prevent dirt and debris from escaping, enhancing the overall efficiency of these cleaning devices.
3. Custom Molding Solutions
Many businesses require custom molds for their products. Silicone membranes offer manufacturers the versatility they need to create unique shapes and sizes tailored to specific needs. This customization is particularly useful in short production runs and prototypes.
How to Choose the Right Silicone Membrane
Selecting the right silicone membrane for your vacuum forming process is crucial for achieving optimal results. Here are several factors to consider:
1. Thickness of the Membrane
The thickness of the silicone membrane impacts its durability and flexibility. Thicker membranes are sturdier but may not conform as well to complex shapes. Conversely, thinner membranes are more flexible and can mold into intricate designs but may wear out faster.
2. Temperature Resistance
Different applications may require membranes that can withstand varying temperature ranges. Ensure that the silicone you choose is suitable for the highest temperature your process demands.
3. Chemical Compatibility
If the materials you are working with involve chemicals, it is imperative to select silicone membranes that resist these substances to avoid chemical degradation.
4. Vacuum Reliability
Evaluate the vacuum sealing capabilities of the membrane. A good silicone membrane should provide a strong, reliable seal during the forming process, preventing air leaks.
Maintenance and Care for Silicone Membrane
To ensure the longevity of silicone membranes used in vacuum forming, proper maintenance is necessary. Here are some essential tips:
- Regular Cleaning: After each use, clean the membranes with a mild detergent and warm water. Avoid abrasive cleaners that could damage the surface.
- Inspect for Damage: Regularly check for tears or wear and replace the membranes as necessary to maintain product quality.
- Store Properly: Store silicone membranes flat in a cool, dry place to prevent distortion.
Future Trends in Vacuum Forming and Silicone Membranes
The industry is moving towards more advanced and efficient production methods. Here are some trends to watch for:
1. Eco-Friendly Materials
With a growing emphasis on sustainability, the demand for eco-friendly silicone membranes is rising. Manufacturers are developing biodegradable or recyclable options that maintain the same high performance.
2. Automation and Smart Manufacturing
Automation technology is increasingly being integrated into the vacuum forming process, enhancing precision and reducing labor costs. This trend will likely continue, allowing for faster production cycles and higher output.
3. Customization and 3D Printing
As 3D printing technology evolves, the ability to create customized molds for vacuum forming may become more accessible. This will further increase the versatility of products created using silicone membranes.
Conclusion
In summary, the silicone membrane for vacuum forming is a vital component in the manufacturing of various appliances and home cleaning products. Its unmatched durability, flexibility, and resistance make it an invaluable asset in achieving quality and efficiency. Businesses in the manufacturing sector that leverage silicone membranes can enhance their product offerings and stay competitive in an ever-evolving market.
As the industry progresses, staying informed about the latest trends and innovations in silicone membranes will enable businesses to adapt and thrive. Whether improving existing products or exploring new opportunities, understanding the role of silicone membranes in vacuum forming is essential for success in today's manufacturing landscape.